Proceso de moldeo por inyección de plástico: Guía completa y aplicaciones
5/1/202526 min leer
El proceso de moldeo por inyección de plástico es una técnica de fabricación ampliamente utilizada en la industria. Consiste en la inyección de material plástico fundido en un molde, donde se enfría y solidifica para formar productos específicos. Este método se caracteriza por su alta precisión y eficiencia en la producción de piezas. A lo largo del artículo, se abordarán las fases del proceso, los materiales utilizados y las aplicaciones en diferentes sectores industriales.
Definición y Principios Básicos del Moldeo por Inyección de Plástico
El moldeo por inyección de plástico es una técnica de fabricación ampliamente utilizada en la industria moderna. Este método permite la producción eficiente y precisa de piezas de plástico a través de un proceso que combina diversas etapas técnicas.
Concepto de Moldeo por Inyección
El proceso de moldeo por inyección consiste en la transformación de material plástico en estado sólido a su forma líquida mediante la aplicación de calor. Este material fundido se inyecta a alta presión en un molde, donde se enfría y solidifica, obteniendo así el producto final con la forma deseada. Es un método que ofrece una excelente repetibilidad, lo que significa que se pueden producir miles de piezas idénticas con alta precisión. Este método es especialmente adecuado para la producción en masa de componentes complejos, destacándose por su capacidad para generar diseños intrincados y formas elaboradas.
Historia y Evolución del Moldeo por Inyección
El moldeo por inyección tiene sus raíces en el siglo XIX. La invención del primer aparato de inyección se atribuye a John Wesley Hyatt, quien patentó un dispositivo en 1872 que permitía inyectar un material plástico primitivo. Desde entonces, esta tecnología ha evolucionado de forma significativa.
Años 20-30: Se introdujeron los primeros compuestos plásticos termoplásticos, lo que amplió las posibilidades del moldeo por inyección a diferentes formas y aplicaciones.
Años 50-60: La popularidad del moldeo por inyección creció enormemente con la disponibilidad de nuevos tipos de plásticos, como el polipropileno y el poliestireno. Las máquinas se modernizaron, lo que mejoró la eficiencia y la capacidad de producción.
Años 80 en adelante: Con la incorporación de tecnología informática y sistemas de control numérico por computadora (CNC), el proceso se volvió más preciso y automatizado, permitiendo un control mejorado de los parámetros del proceso y garantizando una calidad constante en la producción de piezas.
Comparación con Otros Métodos de Fabricación
El moldeo por inyección suele compararse con otros métodos de fabricación de plásticos, como la extrusión y el moldeo por soplado. Cada uno de estos procesos tiene sus particularidades, ventajas y desventajas.
Extrusión: Este proceso es ideal para la producción continua de formas largas que no requieren molde. A diferencia del moldeo por inyección, la extrusión no puede crear formas complejas con detalles intrincados.
Moldeo por Soplado: Utilizado principalmente para producir botellas y envases, este método se basa en la formación de una burbuja de material plástico que se moldea a través de aire. Aunque es efectivo para ciertas aplicaciones, el moldeo por inyección ofrece una mayor precisión dimensional.
Impresión 3D: Un proceso más reciente que permite crear objetos a partir de modelos digitales. Aunque ofrece gran flexibilidad de diseño y reduce el desperdicio de material, la velocidad de producción en comparación con el moldeo por inyección es generalmente menor.
Fases del Proceso de Moldeo por Inyección
El moldeo por inyección se lleva a cabo en una serie de fases interdependientes que garantizan la creación de productos plásticos con las características necesarias. Estas fases son esenciales para asegurar la calidad y la eficiencia del proceso de manufactura.
Alimentación del Material
La primera etapa del proceso implica la correcta alimentación del material plástico que se utilizará. Los pellets de plástico se introducen en el sistema de inyección, donde se preparan para el siguiente paso. Este proceso se realiza a través de una tolva que permite el flujo controlado del material.
Tipos de Alimentos de Material
Pellets de Plástico: Son las formas más comunes de material, que se presentan en pequeñas bolitas y son fáciles de manejar y transportar.
Granulados: Similar a los pellets, pero pueden incluir una variedad de tamaños y composiciones para adaptarse a diferentes requisitos de producción.
Polvos: Utilizados en ciertos procesos especiales, permiten una mezcla más homogénea con otros aditivos.
Fusión y Mezcla
Una vez que el material ha sido alimentado, se procede a la fusión y mezcla. En esta fase, el material plástico se calienta hasta alcanzar su punto de fusión. Este calentamiento se logra utilizando elementos calefactores ubicados en la unidad de inyección.
El tornillo sin fin o husillo juega un papel crucial en esta etapa, ya que no solo funde el material, sino que también lo mezcla adecuadamente para asegurar que se obtenga una composición uniforme.
Inyección del Material Fundido
La fase de inyección es donde el plástico fundido se introduce en el molde. Este paso es crítico para definir las características de la pieza final, así como su precisión dimensional. Una vez que el material es inyectado, se mantiene en el molde por un tiempo determinado para permitir la formación adecuada.
Unidad de Inyección
La unidad de inyección es una parte fundamental de la máquina de moldeo por inyección. Esta unidad se encarga de controlar la cantidad de material inyectado y la velocidad a la que se inyecta. Los parámetros de esta unidad son cruciales para el éxito del proceso.
Enfriamiento y Solidificación
Después de la inyección, se lleva a cabo el enfriamiento y la solidificación del material. Esta fase es crítica, ya que garantiza que la pieza mantenga la forma deseada y evite deformaciones. Durante este tiempo, el molde se mantiene cerrado y se aplica una presión constante.
Parámetros de Enfriamiento
Los parámetros de enfriamiento incluyen la temperatura del molde, el tiempo de enfriamiento y el tipo de refrigeración utilizada. Un enfriamiento adecuado es esencial para evitar defectos en la pieza moldeada y para asegurar su resistencia.
Expulsión de la Pieza Moldeada
Una vez que el material se ha enfriado y solidificado, se procede a la expulsión de la pieza moldeada. Este paso puede realizarse mediante diversos métodos dependiendo del diseño del molde y la forma de la pieza.
Técnicas de Expulsión
Sistemas de Expulsión Mecánica: Utilizan mecanismos como eyectores que empujan la pieza fuera del molde.
Tecnicismo de Expulsión Neumática: Utilizan aire comprimido para ayudar a liberar la pieza del molde.
Sistemas de Vacío: Se emplean en piezas complejas donde el vacío ayuda a soltar la pieza con suavidad.
Materiales Utilizados en el Moldeo por Inyección
La elección de materiales en el moldeo por inyección es fundamental para garantizar la calidad y funcionalidad de los productos finales. Los materiales más comunes en este proceso son los termoplásticos y los elastómeros, aunque también se utilizan bioplásticos y materiales termoplásticos especiales.
Termoplásticos
Los termoplásticos son polímeros que se caracterizan por su capacidad de ser fundidos y moldeados repetidamente sin sufrir cambios químicos. Esto los convierte en una opción popular para el moldeo por inyección, ya que permiten la producción de piezas homogéneas y con alta precisión. Algunos de los termoplásticos más utilizados son:
Polietileno (PE)
El polietileno es uno de los plásticos más comunes y se emplea en una amplia variedad de productos. Se caracteriza por su resistencia a los impactos y a la humedad. Es utilizado en envases, bolsas y componentes eléctricos, entre otros. Según su densidad, se clasifica en polietileno de baja densidad (LDPE) y polietileno de alta densidad (HDPE), cada uno con propiedades específicas que los hacen adecuados para diferentes aplicaciones.
Polipropileno (PP)
El polipropileno es un termoplástico versátil que presenta una buena resistencia química, térmica y a la abrasión. Su ligereza y facilidad de moldear lo convierten en la elección preferida para productos que requieren un equilibrio entre rigidez y flexibilidad. Es comúnmente utilizado en envases, tapones, componentes automotrices y productos textiles.
Poliestireno (PS)
El poliestireno es un material económico y fácil de procesar, ampliamente utilizado en la fabricación de envases rígidos y productos de un solo uso. Se puede presentar en diferentes formas, como poliestireno expandido (EPS) para aplicaciones de embalaje y aislamiento, o poliestireno cristal, que ofrece claridad y apariencia estética, siendo utilizado en productos de consumo como juguetes y electrodomésticos.
Acrilonitrilo Butadieno Estireno (ABS)
El ABS es un terpolímero que combina la rigidez del acrilonitrilo con la resistencia al impacto de butadieno, lo que lo hace ideal para aplicaciones que requieren durabilidad. Este material es comúnmente empleado en la fabricación de carcasas para dispositivos electrónicos, componentes de automóviles y juguetes, gracias a su capacidad para ser moldeado en formas complejas con buena definición.
Elastómeros
Los elastómeros son polímeros con propiedades elásticas, lo que les permite estirarse y recuperar su forma original. Esta característica los hace una excelente opción para aplicaciones que requieren flexibilidad y resistencia al desgaste. En el moldeo por inyección, se emplean comúnmente elastómeros termoplásticos (TPE), que combinan las propiedades de los plásticos y los cauchos, siendo ideales para productos que requieren un tacto suave y una excelente durabilidad, como piezas automotrices y productos médicos.
Materiales Termoplásticos Especiales
Los materiales termoplásticos especiales son aquellos que poseen características específicas para aplicaciones de alto rendimiento. Estos materiales pueden presentar propiedades mejoradas, como mayor resistencia a temperaturas extremas, a productos químicos o al fuego. Son utilizados en sectores que requieren estándares estrictos, como la electrónica, la automoción y el aeroespacial. Ejemplos incluyen poliamidas (nylon), polímeros fluorados y policarbonatos.
Bioplásticos
Los bioplásticos están diseñados para ser más sostenibles y se producen a partir de recursos renovables. Estos materiales pueden ser biocompatibles y, en muchos casos, biodegradables, lo que les otorga ventajas en términos de impacto ambiental. En el moldeo por inyección, se están utilizando bioplásticos como el ácido poliláctico (PLA) y el polihidroxialcanoato (PHA), que son apropiados para aplicaciones que buscan reducir la huella de carbono y promover prácticas sostenibles en la industria.
Maquinaria del Moldeo por Inyección
La maquinaria utilizada en el moldeo por inyección es esencial para garantizar la eficiencia y la calidad en la producción de piezas de plástico. Existen diferentes tipos de máquinas, cada una con características que se adaptan a diversas necesidades industriales.
Máquinas Motorizadas
Las máquinas motorizadas son reconocidas por su precisión y control avanzado. Estas máquinas utilizan servomotores para gestionar el movimiento tanto del tornillo como de la unidad de cierre, lo que permite un ajuste más fino en el proceso de inyección.
Componentes Principales
Unidad de Inyección: Encargada de fundir el material plástico y transportarlo al molde a alta presión.
Unidad de Cierre: Mantiene el molde cerrado durante la inyección, evitando fugas de material.
Controlador Electrónico: Permite la monitorización y ajuste de los parámetros del proceso en tiempo real.
Máquinas Hidráulicas
Las máquinas hidráulicas son una opción popular en el moldeo por inyección, especialmente para piezas de gran tamaño. Funcionan a través de motores hidráulicos que generan una gran fuerza de cierre, lo que resulta esencial en la creación de moldes más grandes y complejos.
Ventajas y Desventajas
Ventajas:
Alta fuerza de cierre, ideal para producciones voluminosas.
Capacidad para trabajar con moldes de grandes dimensiones.
Desventajas:
Consumo energético elevado comparado con modelos motorizados.
Menor precisión en el control de ciertos parámetros del proceso.
Máquinas Híbridas
Las máquinas híbridas combinan tecnología hidráulica y motorizada, reuniendo las ventajas de ambos tipos. Esta combinación mejora la eficiencia energética y proporciona un control preciso sobre el proceso de inyección.
Combinación de Tecnologías
El sistema híbrido permite que la unidad de inyección funcione con elementos eléctricos mientras que la unidad de cierre opera de manera hidráulica. Esto se traduce en un menor consumo energético y un funcionamiento más uniforme.
Mantenimiento de la Maquinaria
El mantenimiento regular de la maquinaria es crucial para asegurar su correcto funcionamiento y prolongar su vida útil. Se recomienda establecer un horario de mantenimiento preventivo que incluya revisiones periódicas de componentes clave.
Inspección de Componentes: Verificar el estado de piezas como el tornillo, la boquilla y los moldes.
Limpieza Regular: Mantener las áreas de trabajo y los sistemas internos limpios para evitar residuos que puedan afectar el proceso.
Calibración: Ajustar los parámetros de la máquina según las especificaciones para prevenir errores en la producción.
Componentes de las Máquinas de Moldeo por Inyección
Las máquinas de moldeo por inyección están compuestas por varios componentes fundamentales que permiten su correcto funcionamiento. Estos componentes son esenciales para garantizar la calidad y la precisión en la producción de piezas plásticas.
Unidad de Inyección
La unidad de inyección es uno de los elementos más críticos de la máquina. Su función principal es fundir y transportar el material plástico al molde. Este componente se encarga de convertir los pellets de plástico en un fluido viscoso, adecuado para ser inyectado. La eficacia de la unidad de inyección influye directamente en la calidad del producto final.
Alimentación de Material: Suele utilizarse una tolva para introducir el plástico en la unidad. El material se calienta y se mezcla a medida que se transporta hacia la cámara de inyección.
Control de Temperatura: La unidad de inyección dispone de un sistema para regular la temperatura, asegurando el correcto estado del material durante toda la fase de inyección.
Presión de Inyección: Este componente también debe generar la presión necesaria para inyectar el material fundido en el molde. La presión adecuada es crucial para evitar defectos en la pieza moldeada.
Unidad de Cierre
La unidad de cierre es igualmente importante, ya que asegura que el molde permanezca cerrado durante el proceso de inyección. Este componente previene fugas de material y garantiza que la presión se mantenga durante la inyección.
Tipo de Sistema: Existen diferentes tipos de sistemas de cierre, ya sean mecánicos o hidráulicos, y cada uno tiene sus propias ventajas y desventajas en términos de fuerza y velocidad de operación.
Mantenimiento: El correcto mantenimiento de la unidad de cierre es fundamental para asegurar su durabilidad y funcionamiento óptimo. El desgaste de las piezas puede afectar la presión de cierre y, por lo tanto, la calidad del producto final.
Moldes
Los moldes son una de las partes más críticas en el proceso de moldeo por inyección. Se fabrican de acuerdo con las especificaciones del producto que se desea crear, y su diseño determina la calidad y precisión de las piezas moldeadas. La fabricación de moldes implica un alto grado de competencia técnica y experiencia.
Diseño del Molde
El diseño del molde debe tener en cuenta varios factores, como el flujo del material, el enfriamiento y la expulsión de la pieza moldeada. Un buen diseño contribuye a una producción eficiente y minimiza el riesgo de defectos. La utilización de software de diseño asistido por ordenador (CAD) es común en esta etapa para crear moldes complejos y precisos.
Moldes de Múltiples Cavidades
Los moldes de múltiples cavidades permiten producir varias piezas en un solo ciclo de inyección. Esto aumenta la eficiencia de producción y reduce costos. La distribución del material en el molde debe ser homogénea para evitar diferencias en la calidad de las piezas. La complejidad en el diseño de estos moldes es mayor, pero resulta beneficioso en términos de productividad.
Diseño de Moldes
El diseño de moldes es una fase crítica en el proceso de moldeo por inyección. Un molde bien diseñado puede influir significativamente en la calidad de las piezas producidas y en la eficiencia del proceso. A continuación, se describen los aspectos fundamentales del diseño de moldes y su relevancia en la fabricación.
Principios Básicos de Diseño
El diseño de un molde debe tener en cuenta varios principios que afectan su funcionalidad y eficacia. Un buen diseño no solo optimiza la producción, sino que también reduce los costos operativos y minimiza los defectos en las piezas. Algunos principios básicos incluyen:
Simetría y Equilibrio: Un molde equilibrado asegura una distribución uniforme del material, lo que ayuda a evitar llenados desiguales y defectos en la pieza final.
Ajuste de Tolerancias: Deben establecerse tolerancias adecuadas en el diseño del molde para garantizar que las piezas moldeadas cumplan con las especificaciones requeridas.
Facilidad de Mantenimiento: Los moldes deben diseñarse de tal manera que su mantenimiento resulte sencillo, con acceso fácil a las piezas que pueden necesitar reparaciones o ajustes.
Consideración de Expansión Térmica: Los materiales de moldes deberán tener en cuenta la expansión térmica durante el calentamiento y enfriamiento del proceso de inyección.
Flujos del Material
El flujo del material es un aspecto esencial en el diseño del molde que afecta directamente el rendimiento durante el moldeo. La manera en que el material fluye influye en la calidad de la pieza moldeada y en los tiempos de ciclo de producción. A considerar:
Canales de Alimentación: Deben diseñarse para permitir un flujo suave y rápido del material hacia las cavidades del molde, evitando obstrucciones que puedan afectar la producción.
Distribución del Material: La geometría del molde debe facilitar que el material llegue a todas las partes de la cavidad de manera uniforme, asegurando así una solidificación consistente.
Optimización de la Viscosidad: El diseño de los canales debe tener en cuenta la viscosidad del material utilizado, lo que puede afectar el llenado del molde.
Diseño para Facilitación de Expulsión
Una expulsión eficiente de la pieza moldeada es vital para mantener el ciclo de producción. Un diseño que favorezca este proceso puede prevenir daños en las piezas y facilitar reparaciones en los moldes. Los aspectos a considerar incluyen:
Ángulos de Desmoldeo: Es esencial incorporar ángulos de desmoldeo adecuados en el diseño del molde para facilitar la expulsión de la pieza al finalizar el ciclo.
Uso de Elementos de Expulsión: Incluir componentes como varillas, placas o ejectores en un diseño adecuado puede ayudar a liberar las piezas sin causar daños.
Minimización de Fricción: Seleccionar materiales adecuados y diseñar superficies con bajo coeficiente de fricción contribuye a una expulsión más eficiente, evitando atascos.
Control y Parametrización del Proceso
El control y la parametrización son aspectos fundamentales en el moldeo por inyección. Ajustes precisos permiten optimizar la calidad del producto final y la eficiencia del proceso. Entre los factores críticos se encuentran la temperatura, la presión y los tiempos de ciclo.
Control de Temperatura
El control de la temperatura es vital en el proceso de moldeo por inyección. La temperatura del material plástico durante la fusión y la inyección afecta directamente a la calidad de las piezas y su integridad estructural.
Los factores a considerar incluyen:
Temperatura de fusión: Esta debe ser lo suficientemente alta para garantizar que el material se vuelva fluido, pero no tanto como para degradar el polímero. Cada tipo de plástico tiene un rango óptimo.
Temperatura del molde: Debe ser controlada para permitir un enfriamiento uniforme del material. Un molde demasiado frío puede causar una solidificación rápida que puede generar defectos en la pieza.
Variaciones de temperatura: Importante monitorizar constantemente para evitar fluctuaciones que puedan comprometer la calidad del producto.
Control de Presión
La presión juega un papel crucial en el proceso de inyección. Asegura que el material fluya adecuadamente en el molde y que se mantenga la forma durante el enfriamiento.
Aspectos a tener en cuenta son:
Presión de inyección: Debe ser suficiente para llenar el molde completamente antes de que el material empiece a enfriarse y solidificarse. Un exceso de presión puede provocar defectos, como la aparición de marcas de refrigeración.
Presión de cierre: Esta asegura que el molde permanezca sellado durante la inyección, evitando fugas. Debe ser calibrada según el tamaño y la configuración del molde.
Medidores de presión: Estos dispositivos deben ser utilizados para una monitorización constante, permitiendo ajustes en tiempo real para mantener la calidad del proceso.
Tiempos de Ciclo
El tiempo de ciclo se refiere al tiempo total necesario para completar una producción de una pieza. Este incluye el tiempo de inyección, enfriamiento y expulsión, y debe ser optimizado para mejorar la eficiencia del proceso.
Los elementos a considerar son:
Tiempo de inyección: Cuanto más rápido se inyecte el material, menor será el riesgo de problemas de llenado. Sin embargo, un tiempo demasiado corto puede comprometer la calidad de la pieza.
Tiempo de enfriamiento: Este es crítico para asegurar que la pieza adquiera las propiedades mecánicas deseadas. La duración debe ser ajustada según el tipo de material utilizado y el espesor de las piezas.
Tiempo de expulsión: Este consiste en el período necesario para que la pieza moldeada sea expulsada del molde y debe ser optimizado para evitar retrasos en la producción.
Aplicaciones del Moldeo por Inyección
El moldeo por inyección es ampliamente utilizado en diversas industrias debido a su versatilidad y capacidad para producir piezas de alta precisión. A continuación, se detallan algunas de las aplicaciones más relevantes.
Industria Automotriz
En la industria automotriz, el moldeo por inyección juega un papel crucial en la fabricación de numerosos componentes. Este proceso permite la producción en masa de piezas complejas a un coste relativamente bajo y con alta eficiencia.
Componentes de Automóviles
Los componentes automotrices fabricados mediante este método incluyen:
Paneles exteriores e interiores, como parachoques y carcasas.
Bandejas y soportes que contribuyen a la estructura de los vehículos.
Componentes eléctricos, como conectores y carcasas de interruptores.
Elementos de seguridad, incluyendo airbag y piezas relacionadas.
La precisión en la fabricación asegura que estas piezas se ajusten perfectamente y cumplan con las estrictas normativas de calidad y seguridad de la industria.
Electrónica de Consumo
El sector de la electrónica de consumo también se beneficia enormemente del moldeo por inyección. Este proceso permite la producción rápida y eficiente de carcasas y componentes que cumplen con los requisitos técnicos y estéticos requeridos.
Carcasas de teléfonos móviles y dispositivos electrónicos.
Conectores y componentes internos que requieran aislamiento eléctrico.
Controles, botones y paneles de acceso de diversos dispositivos.
Estas aplicaciones demandan una alta precisión y una excelente terminación superficial, que el moldeo por inyección es capaz de ofrecer.
Productos de Consumo Diarios
El moldeo por inyección también se utiliza para la fabricación de numerosos productos de uso cotidiano. La capacidad para producir grandes volúmenes de productos a un coste razonable es una de las razones de su popularidad en este sector.
Utensilios de cocina, como platos, tazas y cubiertos.
Toys y juguetes de plástico, que requieren seguridad y durabilidad.
Envases de diversos tipos, desde botellas hasta recipientes almacenaje.
La diversidad de diseños y materiales que se pueden utilizar permite a los fabricantes innovar y adaptar los productos a las tendencias del mercado.
Sector Médico
En el ámbito médico, el moldeo por inyección es indispensable para la creación de componentes que deben cumplir con estándares estrictos de higiene y eficacia.
Piezas para dispositivos médicos, como jeringas y tubos.
Componentes de equipos de diagnóstico, que requieren alta precisión y fiabilidad.
Envases para productos farmacéuticos, asegurando condiciones seguras para el almacenamiento.
El uso de materiales biocompatibles y la capacidad de producir en series reducidas son características que hacen del moldeo por inyección un proceso preferido en este sector.
Ventajas del Moldeo por Inyección
El moldeo por inyección ofrece diversas ventajas que lo convierten en un método preferido en la fabricación industrial. Estas ventajas abarcan desde la precisión en la producción, hasta la reducción de residuos y la flexibilidad en el diseño de productos.
Alta Precisión
Una de las características más destacadas del moldeo por inyección es su capacidad para producir piezas con alta precisión dimensional. Esto es posible gracias a los moldes que se utilizan, los cuales pueden ser diseñados con tolerancias muy ajustadas. El resultado es una producción constante de componentes que cumplen con las especificaciones requeridas. La precisión en el moldeo por inyección se traduce en:
Fabicación de piezas idénticas.
Minimización de errores en la producción.
Reducción de la necesidad de ajustes posteriores.
Baja Generación de Residuos
El moldeo por inyección es conocido por su eficiencia en la utilización de materiales. Este método genera mínimas pérdidas de material durante el proceso de producción, lo que es beneficioso tanto para la economía de la empresa como para el medio ambiente. Las características que contribuyen a esta baja generación de residuos incluyen:
Recuperación y reutilización de material sobrante.
Proceso de inyección preciso que utiliza solo la cantidad necesaria de plástico.
Optimización del diseño del molde para maximizar la utilización del material.
Flexibilidad en el Diseño
La flexibilidad es otra ventaja clave del moldeo por inyección. Este proceso permite realizar ajustes y cambios en el diseño de los moldes con facilidad, lo que significa que se pueden producir diferentes tipos de productos sin necesidad de invertir en nuevas máquinas. Esta flexibilidad ofrece:
Capacidad para adaptar los moldes a diferentes especificaciones sin complicaciones.
Producción de una gama amplia de productos desde una misma máquina.
Facilita la personalización de productos según las demandas del mercado.
Producción a Gran Escala
El moldeo por inyección es altamente eficiente para la producción en masa. Una vez que se ha fabricado el molde, se pueden producir miles de piezas en un período de tiempo relativamente corto. Esta característica es crucial para industrias que demandan grandes cantidades de productos, como la automotriz o la de consumo. Las ventajas asociadas a la producción a gran escala incluyen:
Reducción de los costos por unidad a medida que aumenta la producción.
Comunicación efectiva con la cadena de suministro para cumplir con los plazos de entrega.
Capacidad de respuesta a la demanda del mercado creciente.
Desafíos del Moldeo por Inyección
El moldeo por inyección presenta diversos desafíos que pueden afectar la calidad del producto final, la eficiencia del proceso y los costos operativos. Estos retos requieren atención especial para asegurar la efectividad del proceso y la viabilidad comercial de las piezas producidas.
Defectos Comunes en las Piezas
Uno de los principales desafíos en el moldeo por inyección son los defectos que pueden presentarse en las piezas moldeadas. Estos fallos no solo impactan la calidad del producto final, sino que también pueden resultar en desperdicios materiales y aumentar los costos de producción. Entre los defectos más frecuentes se encuentran:
Rupturas o grietas.
Deformaciones o distorsiones.
Fugas de material.
Superficies rugosas o con imperfecciones.
Inyección incompleta.
Soluciones a Defectos
Para resolver los defectos que pueden surgir durante el proceso de moldeo por inyección, se implementan diversas estrategias. Cada tipo de defecto requiere un enfoque específico:
Rupturas o grietas: Se pueden prevenir ajustando los parámetros de enfriamiento y asegurando una mezcla uniforme del material plástico.
Deformaciones o distorsiones: Un diseño óptimo del molde y la control de la temperatura durante la inyección ayudan a minimizar este problema.
Fugas de material: Asegurar un cierre adecuado del molde es crucial para evitar pérdidas de plástico.
Superficies rugosas o con imperfecciones: La calidad del molde y el tratamiento de su superficie son aspectos determinantes para conseguir acabados lisos.
Inyección incompleta: La calibración de la presión de inyección y del tiempo de retención puede mejorar el llenado del molde.
Costos Iniciales de Implementación
Otro desafío significativo asociado al moldeo por inyección son los altos costos iniciales de implementación. Estos costos pueden abarcar diversas áreas, como la adquisición de maquinaria y moldes, así como la inversión en infraestructura y capacitación del personal. Algunos factores específicos que influyen en estos costos son:
Precio del equipo de moldeo por inyección, que puede ser elevado dependiendo de la tecnología y las características deseadas.
Desarrollo y fabricación de moldes personalizados, que a menudo requieren inversiones significativas de tiempo y recursos.
Formación del personal, que es fundamental para operar la maquinaria de manera eficiente y evitar errores costosos durante la producción.
Complejidad del Mantenimiento
El mantenimiento de las máquinas de moldeo por inyección es otro aspecto complejo que puede influir en la eficiencia y la rentabilidad del proceso. Las máquinas requieren un mantenimiento regular para garantizar su funcionamiento óptimo y evitar paradas imprevistas en la producción. Los principales desafíos en este ámbito incluyen:
Reparaciones de componentes críticos, que pueden ser costosas y requieren tiempo de inactividad.
Necesidad de revisiones periódicas y calibraciones que aseguren la precisión de las máquinas.
Acceso a repuestos de calidad, que no siempre están disponibles de manera inmediata, lo que puede alargar los tiempos de mantenimiento.
Perspectivas Futuras del Moldeo por Inyección
El futuro del moldeo por inyección se perfila con oportunidades emocionantes en el ámbito de los materiales, los avances tecnológicos y la sostenibilidad. La industria está en constante evolución, adaptándose a las nuevas demandas del mercado y ofreciendo soluciones innovadoras para desafíos emergentes.
Tendencias en Materiales
El desarrollo de nuevos materiales está jugando un papel crucial en la redefinición del moldeo por inyección. Con la creciente necesidad de productos más sostenibles y eficientes, los siguientes tipos de materiales están ganando relevancia:
Bioplásticos: Estos materiales, elaborados a partir de fuentes renovables, están siendo cada vez más utilizados en el moldeo por inyección. Su capacidad compostable y biodegradabilidad está transformando la manera en la que las empresas piensan sobre el ciclo de vida de sus productos.
Termoplásticos de alto rendimiento: Estos plásticos ofrecen propiedades mecánicas superiores y pueden soportar temperaturas más elevadas. Esto los hace ideales para aplicaciones en sectores como la automoción y la electrónica.
Materiales reciclados: La recuperación y reutilización de plásticos reciclados está en aumento, reduciendo la dependencia de recursos vírgenes y disminuyendo el impacto ambiental. Su uso es una tendencia creciente que ayuda a cumplir con las normativas de sostenibilidad.
Avances Tecnológicos
La tecnología continúa avanzando, lo que permite optimizar el proceso de moldeo por inyección. Las tendencias actuales incluyen:
Automatización y robótica: La implementación de sistemas automatizados mejora la precisión y reduce el tiempo de ciclo. Los robots colaborativos son cada vez más comunes en la extracción de piezas y en el manejo de materiales.
Control digital y análisis de datos: La recopilación y análisis de datos en tiempo real ayudan a monitorear el proceso y a hacer ajustes instantáneos, mejorando la calidad del producto final.
Desarrollo de software de simulación: Las herramientas de simulación permiten predecir el comportamiento del material en el molde, facilitando el diseño y la mejora de los procesos antes de la producción física.
Sostenibilidad y Economía Circular
La sostenibilidad se ha convertido en una prioridad clave en la industria del moldeo por inyección. Las iniciativas para promover una economía circular están impulsando cambios significativos:
Reducción de residuos: Se están implementando técnicas para minimizar el desperdicio durante el proceso de producción, como el reciclaje de materiales y la optimización de los ciclos de producción.
Uso de energía renovable: Muchas empresas están adoptando fuentes de energía sostenible, como la solar y eólica, para alimentar sus instalaciones de producción, reduciendo así su huella de carbono.
Educación y concienciación: La industria está abogando por una mayor sensibilización sobre la gestión de residuos plásticos, fomentando prácticas responsables entre consumidores y fabricantes.
Normativas y Estándares de Calidad
Las normativas y estándares de calidad en el moldeo por inyección son esenciales para garantizar la seguridad, funcionalidad y sostenibilidad de los productos fabricados. Estas regulaciones son establecidas tanto a nivel nacional como internacional, asegurando que las técnicas de producción sean seguras y eficientes.
Regulaciones Internacionales
Las regulaciones internacionales proporcionan un marco normativo común que las empresas deben seguir para asegurar la calidad y seguridad de los productos fabricados. Estas normas son esenciales para operar en mercados globales y suelen estar alineadas con las mejores prácticas de la industria.
ISO (Organización Internacional de Normalización)
La ISO 9001 establece criterios para la gestión de calidad en la producción. Esto incluye procesos de mejora continua y el enfoque al cliente.
La ISO 14001 se centra en la gestión ambiental, garantizando que las prácticas de fabricación reduzcan el impacto ambiental.
La ISO 45001 proporciona normas para la gestión de la salud y la seguridad en el trabajo, protegiendo a los trabajadores en el entorno de fabricación.
ASTM (Sociedad Americana para Pruebas y Materiales)
ASTM D638 determina las propiedades mecánicas de materiales plásticos mediante ensayos de tracción.
ASTM D790 se utiliza para evaluar la flexión de materiales plásticos, lo cual es crucial en aplicaciones de carga.
CE (Conformidad Europea)
El marcado CE es requerido para productos vendidos en el Espacio Económico Europeo, indicando que el producto cumple con las normativas de seguridad y salud aplicables.
Certificaciones y Normas de Calidad
Las certificaciones son esenciales para demostrar que una empresa cumple con ciertos estándares de calidad. Estas pueden ser requeridas tanto por clientes como por regulaciones gubernamentales. Las siguientes certificaciones son relevantes en la industria del moldeo por inyección:
Certificación ISO 13485
Específica para dispositivos médicos, esta norma garantiza la calidad y seguridad de los productos, empezando desde el diseño hasta la fabricación.
Certificación IATF 16949
Es un estándar para sistemas de gestión de calidad en la industria automotriz, asegurando la mejora continua en la producción de componentes.
Certificaciones de Sostenibilidad
Certificaciones como la norma ISO 50001 ayudan a las empresas a gestionar su energía de manera eficaz, promoviendo la sostenibilidad en el proceso de producción.
Impacto Ambiental del Moldeo por Inyección
El impacto ambiental del moldeo por inyección es un tema relevante en la actualidad. Este proceso, aunque eficiente, presenta desafíos que deben abordarse para minimizar su impacto en el entorno.
Gestión de Residuos Plásticos
La gestión de residuos plásticos es fundamental en el contexto del moldeo por inyección. Los desechos generados durante la producción pueden tener efectos perjudiciales en el medio ambiente si no se manejan adecuadamente. Implementar sistemas eficaces de gestión de residuos es crucial. Algunos métodos incluyen:
Reciclaje de los recortes: Los restos de material plástico generados durante el proceso pueden ser reciclados y reutilizados en nuevas producciones.
Reutilización: Las piezas defectuosas pueden ser reprocesadas mediante técnicas adecuadas para su reincorporación en la cadena de producción.
Disposición responsable: Es esencial contar con procesos de disposición de desechos que cumplan con las normativas ambientales, evitando la contaminación del suelo y agua.
Uso de Materiales Reciclados
El uso de materiales reciclados en el moldeo por inyección se ha convertido en una práctica habitual para reducir la dependencia de recursos vírgenes. Incorporar plásticos reciclados no solo disminuye la huella de carbono, sino que también promueve la economía circular. Entre los beneficios de esta práctica destacan:
Reducción de residuos: Al utilizar materiales reciclados, se disminuye la acumulación de desechos plásticos en vertederos.
Consumo de energía: La producción de plásticos reciclados suele requerir menos energía en comparación con la fabricación de plásticos nuevos.
Innovación en productos: La combinación de materiales reciclados permite la creación de nuevos productos con características mejoradas.
Innovaciones Sostenibles
Las innovaciones sostenibles han emergido como una respuesta a los desafíos ambientales del moldeo por inyección. Estas innovaciones buscan no solo mejorar la eficiencia del proceso, sino también reducir su impacto ambiental. Algunas de las prácticas innovadoras incluyen:
Desarrollo de bioplásticos: Estos materiales, derivados de fuentes renovables, ofrecen alternativas al plástico tradicional y son compostables.
Optimización del proceso de inyección: La implementación de tecnologías avanzadas, como el control numérico por computadora, ayuda a reducir el desperdicio de material y mejorar la precisión.
Uso de energía renovable: Integrar fuentes de energía limpias en las fábricas reduce las emisiones de carbono asociadas con la producción.
Comparación de Técnicas de Moldeo
La comparación de técnicas de moldeo se centra en las diferencias y similitudes entre los métodos utilizados en la fabricación de productos plásticos. A continuación, se presentan las características que distinguen el moldeo por inyección de otras técnicas populares.
Moldeo por Inyección vs. Extrusión
El moldeo por inyección y la extrusión son dos de las técnicas más utilizadas en la producción de artículos de plástico. Cada una tiene sus particularidades, lo que las hace más adecuadas para diferentes aplicaciones.
Principio de funcionamiento:
El moldeo por inyección consiste en inyectar plástico fundido en un molde, donde se enfría y solidifica en la forma deseada.
La extrusión, por otro lado, implica forzar el material plástico fundido a través de un molde de forma continua, creando perfiles o tubos.
Tipos de productos:
El moldeo por inyección es ideal para la producción de piezas complejas y detalladas, como componentes electrónicos y juguetes.
La extrusión se utiliza comúnmente para producir artículos como tuberías, láminas y perfiles que requieren un diseño prolongado y uniforme.
Velocidad de producción:
El moldeo por inyección puede ofrecer ciclos de producción más rápidos una vez que se establece el molde.
La extrusión es continua, lo que permite producir grandes volúmenes de material de manera constante.
Costes iniciales:
El moldeo por inyección generalmente requiere una mayor inversión inicial debido al costo de los moldes personalizados.
La extrusión, en cambio, suele tener costos iniciales más bajos y es más eficiente para producciones a largo plazo de productos sencillos.
Moldeo por Inyección vs. Impresión 3D
La impresión 3D ha ganado popularidad en los últimos años como una alternativa innovadora para la creación de objetos. Compararla con el moldeo por inyección permite entender sus aplicaciones y limitaciones.
Proceso de fabricación:
El moldeo por inyección utiliza moldes para crear piezas a gran escala mediante la inyección de plástico fundido.
La impresión 3D construye objetos capa por capa a partir de un modelo digital, sin necesidad de moldes.
Flexibilidad de diseño:
El moldeo por inyección es limitado a la geometría del molde, lo que puede restringir la complejidad de las piezas producidas.
La impresión 3D permite diseñar formas altamente complejas y personalizadas sin las restricciones de un molde.
Costos:
El moldeo por inyección tiene un alto costo inicial debido a la necesidad de fabricarse moldes personalizados, aunque el coste por pieza disminuye con la producción en masa.
La impresión 3D suele implicar un menor coste inicial, pero los costos por unidad pueden ser más altos, especialmente en grandes volúmenes.
Tiempos de producción:
La producción en moldeo por inyección es rápida una vez que se completa el molde, ideal para grandes cantidades.
La impresión 3D puede ser más lenta, ya que cada objeto se crea capa por capa, pero es más adecuada para prototipos inmediatos.
Moldeo por Inyección vs. Moldeo por Soplado
El moldeo por soplado es otra técnica utilizada frecuentemente en la industria del plástico, especialmente para la producción de recipientes huecos. Aquí se detallan las diferencias con el moldeo por inyección.
Proceso de fabricación:
En el moldeo por inyección, el plástico se inyecta en un molde para crear objetos sólidos.
El moldeo por soplado implica inflar un tubo de plástico fundido dentro de un molde, formando obj
Contacto
alcoy@frogplastics.es
Horario de oficina:
Lunes a Jueves: De 8:00h a 18:00h
Viernes: De 8:00h a 15:00h
Oficina: (+34) 631 687 558
FROG PLASTICS S.L
Llámenos ahora y le atenderemos personalmente, o si lo prefiere, envíenos un whatssap o e-mail y le contestaremos a la mayor brevedad posible.
NIF B-56540388
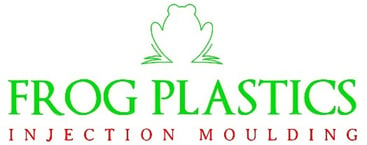
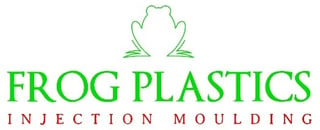
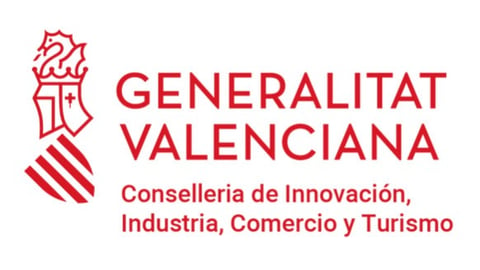
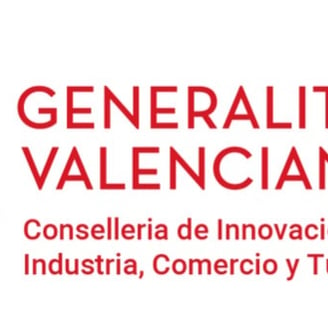
Proyecto subvencionado por la Conselleria de Innovación, Industria, Comercio y Turismo:
“FROG PLASTICS, S.L.” ha participado en el programa de Ayudas para apoyar las inversiones productivas realizadas por las pymes de diversos sectores industriales de la Comunitat Valenciana. RESOLUCIÓN de 15 DE febrero de 2024 (DOGV Num. 9791 / 19.02.2024) a través de la inversión para el proceso de fabricación de piezas por inyección de plástico
Año: 2024 Número de expediente: INPYME/2024/414
Subvención: 34.935,45 €