En qué consiste el moldeo por inyección de plástico y cómo se aplica
3/1/202519 min leer
El moldeo por inyección es un método de fabricación de plásticos que permite producir piezas complejas de manera eficiente. Esta técnica implica fundir resinas y forzarlas en moldes específicos. El proceso consta de varias etapas, desde la preparación del material hasta la expulsión de la pieza final. Su versatilidad y capacidad de producción en masa lo convierten en una opción ampliamente utilizada en diversas industrias.
Descripción General del Moldeo por Inyección
El moldeo por inyección es un proceso clave en la fabricación de productos plásticos. Esta técnica se ha desarrollado a lo largo de los años y se utiliza en una variedad de aplicaciones industriales debido a su eficiencia y versatilidad. A continuación, se presenta una descripción detallada sobre su historia, definición y comparación con otras técnicas de fabricación.
Historia y Origen del Moldeo por Inyección
El moldeo por inyección tiene sus raíces en el siglo XIX. Se originó a partir de la necesidad de producir artículos plásticos de forma más eficiente y rápida. La primera máquina de moldeo por inyección fue patentada en 1872 por John Wesley Hyatt, quien utilizó esta técnica para crear botones de celuloide. A lo largo de los años, la tecnología ha avanzado significativamente, incorporando innovaciones que han permitido mejorar tanto la calidad como la velocidad de producción.
En el siglo XX, la llegada de los termoplásticos revolucionó el sector, permitiendo la fabricación de una amplia gama de productos. Hoy en día, el moldeo por inyección es una técnica ampliamente utilizada en diversas industrias, incluyendo la automotriz, la electrónica y la medicina.
Definición y Principios Básicos
El moldeo por inyección se puede definir como un proceso de fabricación en el que se inyecta material plástico fundido en un molde para crear piezas de formas específicas. Este proceso implica varios pasos: preparación del material, inyección del mismo en el molde, enfriamiento y expulsión de la pieza moldeada.
Los principios básicos del moldeo por inyección incluyen el uso de presión para introducir el material en el molde y la necesidad de enfriamiento para solidificar la pieza. La precisión en el control de las variables del proceso es crucial para garantizar la calidad del producto final.
Comparación con Otras Técnicas de Fabricación
Existen varias técnicas de fabricación que se utilizan en la producción de piezas de plástico. El moldeo por inyección se compara favorablemente con otras metodologías en términos de eficiencia y versatilidad.
Moldeo por Compresión
El moldeo por compresión es un método en el que se coloca un material plástico en un molde caliente y se aplica presión para forzar el material a llenar el molde. A diferencia del moldeo por inyección, este proceso no requiere inyección a alta presión. Sin embargo, el moldeo por compresión puede ser menos preciso y estar limitado a formas menos complejas.
Rotomoldeo
El rotomoldeo es una técnica que implica la rotación del molde mientras se calienta, permitiendo que el material plástico se adhiera a las paredes del molde. Este método es ideal para la producción de piezas huecas y grandes, pero no es tan adecuado para producciones de alta precisión como el moldeo por inyección.
Extrusión
La extrusión consiste en forzar el material plástico a través de una matriz para crear productos de perfil continuo, como tubos o láminas. Aunque es eficaz para ciertos tipos de productos, no permite la misma versatilidad en el diseño que el moldeo por inyección, que puede crear formas complejas y personalizadas de forma más eficiente.
Proceso de Moldeo por Inyección
El proceso de moldeo por inyección comprende varias etapas clave que garantizan la obtención de piezas plásticas con propiedades deseadas. Desde la preparación de los materiales hasta la expulsión de las piezas moldeadas, cada fase es esencial para lograr resultados óptimos en la fabricación.
Preparación de Material
Esta fase se centra en la selección y preparación de las resinas plásticas que se utilizarán en el proceso. El cuidado en esta etapa es fundamental, ya que la calidad del material influye directamente en la calidad del producto final.
Gránulos de Resina Plástica
Los gránulos de resina plástica, también conocidos como pellets, son la forma inicial del material que se utilizará en el moldeo por inyección. Estas resinas se someten a un proceso de calentamiento para que se fundan adecuadamente, permitiendo una correcta inyección en el molde. Existen distintos tipos de resinas que se pueden emplear, como termoplásticos y termofijos, dependiendo de las propiedades requeridas en la pieza final.
Tipos de Tolvas
Las tolvas son sistemas de almacenamiento que facilitan la alimentación de los gránulos al cilindro de inyección. Se presentan en diversas configuraciones, y su diseño puede afectar la eficiencia del proceso. Las tolvas pueden ser:
Tolvas de gravedad: Permiten que los gránulos caigan de manera natural hacia el cilindro.
Tolvas con agitador: Mantienen los gránulos en movimiento para evitar bloqueos y asegurar un flujo constante.
Tolvas climatizadas: Controlan la temperatura del material para mejorar la fluidez durante el proceso de inyección.
Inyección de Material
La inyección es una de las etapas más críticas del proceso, donde el material fundido se introduce en el molde a alta presión. La manera en que se realiza puede afectar significativamente la calidad y consistencia de la pieza producida.
Alta Presión en el Bebedero
Durante la inyección, el material plástico fundido es conducido a través de un canal conocido como bebedero. La presión aplicada en esta fase es fundamental, ya que determina la eficiencia con que el material llena la cavidad del molde. Un control preciso de la presión ayuda a prevenir defectos en la pieza terminada.
Distribución en la Cavidad del Molde
La correcta distribución del material en la cavidad del molde es vital para garantizar que todas las áreas sean llenadas de manera uniforme. La forma del molde, el diseño del bebedero y otros factores como la viscosidad del material influyen en esta fase. Se requiere una atención especial para evitar burbujas de aire y otros defectos que puedan comprometer la integridad de la pieza.
Enfriamiento y Solidificación
Después de que el molde se ha llenado, el siguiente paso es permitir que el material se enfríe y solidifique. Esta etapa es crucial para el acabado final del producto y requiere un control cuidadoso de la temperatura.
Duración del Proceso de Enfriamiento
La duración del enfriamiento varía en función del tipo de material utilizado y la geometría de la pieza. Un enfriamiento demasiado rápido puede causar tensiones internas, mientras que un enfriamiento muy lento puede alargar el ciclo de producción, lo que no es eficiente. Las características térmicas del material usado juegan un papel importante en este aspecto.
Factores que Afectan la Solidificación
Varios factores pueden influir en el proceso de solidificación, incluyendo:
Temperatura inicial del material y del molde.
Espesor de las paredes de la pieza.
Propiedades térmicas del plástico utilizado.
Una correcta comprensión de estos factores es esencial para optimizar el ciclo de moldeo.
Expulsión de la Pieza Moldeada
Una vez que el material ha solidificado completamente, llega el momento de expulsar la pieza del molde. Esta etapa es crucial para evitar daños tanto en la pieza como en el molde.
Sistemas de Expulsión
Los sistemas de expulsión son mecanismos diseñados para sacar la pieza moldeada del molde sin causar daños. Existen diferentes métodos de expulsión, como el uso de ejectores, que aplican presión sobre la pieza al abrir el molde. Estos mecanismos operan de manera sincronizada con el ciclo de moldeo para garantizar una producción fluida.
Recorte de Elementos Sobrantes
Después de la expulsión, es común que queden elementos sobrantes, como el bebedero y los corredores. Estos deben ser recortados para obtener el producto terminado. Este proceso puede hacerse manualmente o a través de soluciones automáticas, dependiendo de la escala de producción y de las especificaciones del producto final.
Máquina de Moldeo por Inyección
La máquina de moldeo por inyección es el corazón del proceso de fabricación, diseñada para transformar gránulos de resina plástica en piezas moldeadas. Su funcionamiento eficiente y su capacidad para adaptarse a distintas configuraciones hacen que este equipo sea esencial en la producción de plásticos.
Unidad de Inyección
La unidad de inyección es responsable de fundir los gránulos de plástico y de inyectar el material fundido en el molde. Esta parte de la máquina juega un papel crítico en la calidad final de la pieza moldeada, ya que cualquier variación en el proceso puede afectar la precisión de la producción.
Máquinas Híbridas
Las máquinas híbridas combinan la tecnología hidráulica y eléctrica, ofreciendo beneficios de ambas. Este tipo de equipo proporciona una energía más eficiente, menor consumo de recursos y una mayor velocidad de respuesta durante el proceso de inyección. Al contar con la versatilidad de ambos sistemas, las máquinas híbridas representan una opción muy atractiva para la producción moderna.
Unidad de Sujeción
La unidad de sujeción es crucial para mantener el molde cerrado durante el proceso de inyección. Esta sección de la máquina asegura que el molde no se abra, lo que evitaría que el material fundido se derrame y comprometa la calidad de la pieza final. La eficacia de esta unidad es fundamental para lograr una producción de alta calidad.
Fuerza de Cierre
La fuerza de cierre se refiere a la capacidad de la máquina para mantener el molde cerrado ante la presión generada durante la inyección. De esta manera, se evita la deformación o el deslizamiento del molde. La selección adecuada de la fuerza de cierre depende del tamaño y la complejidad de las piezas a producir y se mide en toneladas de presión, variando según las especificaciones del molde y el tipo de plástico utilizado.
Tecnología CNC en el Moldeo por Inyección
La tecnología de control numérico computarizado (CNC) se ha integrado en las máquinas de moldeo por inyección para mejorar la precisión y la repetibilidad del proceso. Esta tecnología permite ajustes automáticos en tiempo real, garantizando que cada inyección se realice con las mismas especificaciones. Este avance no solo aumenta la calidad del producto, sino que también reduce el tiempo de configuración y minimiza los desperdicios.
Materiales Utilizados en el Moldeo por Inyección
El moldeo por inyección utiliza una variedad extensa de materiales, principalmente plásticos, que son seleccionados según las características deseadas del producto final. Estos plásticos pueden ser termoplásticos, que ofrecen la ventaja de ser moldeables múltiples veces, asegurando versatilidad y eficiencia en la producción.
Tipos de Plásticos
Dentro del ámbito del moldeo por inyección, existen varios tipos de plásticos que se utilizan para la fabricación de piezas. Estos materiales son seleccionados en función de sus propiedades mecánicas, térmicas y ópticas, así como de su costo y facilidad de procesamiento.
Polietileno (PE)
El polietileno es uno de los plásticos más versátiles y comúnmente utilizados en el moldeo por inyección. Se caracteriza por su flexibilidad, durabilidad y resistencia química. Hay varias variantes del polietileno, incluyendo:
Polietileno de baja densidad (LDPE): Con alta flexibilidad y una buena resistencia a los impactos, es utilizado en productos como bolsas de plástico y películas.
Polietileno de alta densidad (HDPE): Este tipo es más resistente y rígido, lo que lo hace ideal para envases y contenedores que requieren una mayor durabilidad.
Polietileno lineal de baja densidad (LLDPE): Combina propiedades de LDPE y HDPE, siendo versátil para varias aplicaciones que necesitan un equilibrio entre flexibilidad y resistencia.
Otros Materiales Utilizados
Además del polietileno, hay una amplia gama de otros materiales que se emplean en el moldeo por inyección, cada uno con propiedades específicas:
Acrilonitrilo Butadieno Estireno (ABS): Conocido por ser robusto y ligero, se utiliza comúnmente en juguetes, electrodomésticos y componentes automotrices.
Policarbonato: Este material es transparente y extremadamente resistente a impactos, lo que lo hace ideal para aplicaciones como lentes de gafas y cubiertas de dispositivos electrónicos.
Nailon (Poliamida): Destaca por su resistencia y propiedades eléctricas, siendo utilizado en componentes de maquinaria, artículos deportivos y productos de consumo.
Polipropileno (PP): Este plástico es conocido por su flexibilidad y resistencia química, siendo común en envases de alimentos y productos de uso diario.
Poliestireno (PS): Utilizado en empaques y productos desechables, se caracteriza por su facilidad de moldeado y bajo costo de producción.
Ventajas del Moldeo por Inyección
El moldeo por inyección ofrece diversos beneficios que lo convierten en un método preferido en la producción de piezas de plástico. Su efectividad se traduce en rapidez, precisión y versatilidad, lo que le confiere ventajas competitivas en múltiples sectores industriales.
Alta Precisión y Tolerancias Ajustadas
Una de las principales ventajas del moldeo por inyección es su capacidad para producir piezas con altas tolerancias y precisión. Este método permite diseños que requieren ajustes mínimos en las dimensiones, lo cual es crucial en aplicaciones donde la exactitud es fundamental. Las máquinas de moldeo por inyección están diseñadas para asegurar que cada pieza cumpla con especificaciones exigentes, minimizando defectos y variaciones en la producción.
Capacidad de Producción en Masa
El moldeo por inyección es ideal para la fabricación en masa, ya que permite la producción continua de grandes volúmenes de piezas idénticas en un tiempo relativamente corto. Esto se traduce en un proceso altamente eficiente que reduce el tiempo de espera y mejora el flujo de trabajo en las líneas de producción. Consecuentemente, las industrias pueden satisfacer la demanda del mercado con mayor rapidez y eficacia.
Flexibilidad de Diseño
Este método permite la creación de formas complejas y diseños innovadores que podrían ser difíciles de lograr con otras técnicas. Los moldes pueden ser diseñados para incluir características intrincadas, lo que abre un abanico de posibilidades creativas para los diseñadores. Esto se traduce en la capacidad de producir productos con estética y funcionalidad superiores.
Durabilidad y Mejora de Materiales
Los plásticos utilizados en el moldeo por inyección pueden ser modificados con aditivos, lo que mejora sus propiedades físicas. Esto resulta en productos más resistentes, duraderos y capaces de soportar condiciones extremas. La mejora en la durabilidad también reduce los costos a largo plazo, convirtiéndolos en opciones más atractivas para diversas aplicaciones industriales.
Eficiencia Económica
Si bien la inversión inicial en moldes puede ser considerable, el moldeo por inyección permite la reducción de costos por unidad a medida que aumenta la producción. Esta economía de escala hace que el proceso sea muy rentable a largo plazo. Además, el bajo desperdicio de material y la alta tasa de producción contribuyen a la eficiencia económica global del proceso.
Aplicaciones del Moldeo por Inyección
El moldeo por inyección es una técnica utilizada en una variedad de industrias, gracias a su capacidad para producir piezas complejas y de alta precisión en grandes cantidades. A continuación, se describen las principales aplicaciones en diferentes sectores.
Industria Automotriz
En el sector automotriz, el moldeo por inyección desempeña un papel crucial en la producción de diversas piezas que contribuyen a la funcionalidad y estética de los vehículos. Este proceso permite la creación de componentes de alto rendimiento, que se caracterizan por su durabilidad y precisión.
Carcasas y Conectores
Las carcasas de los distintos sistemas de un automóvil, así como los conectores eléctricos, son producidos mediante moldeo por inyección. Estos componentes requieren materiales que ofrezcan resistencia al impacto y al calor, garantizando así un funcionamiento óptimo a lo largo del tiempo. La elevada precisión necesaria en la fabricación de estos elementos hace que el moldeo por inyección sea la opción preferida.
Otros Componentes
Asimismo, el moldeo por inyección es utilizado para fabricar una amplia gama de otros componentes, como paneles interiores, clips y sujetadores. La versatilidad de esta técnica permite la producción en masa de elementos que no solo cumplen funciones estructurales, sino que también mejoran la experiencia del usuario en el vehículo.
Industria Electrónica
La industria electrónica se beneficia en gran medida del moldeo por inyección, ya que permite la fabricación de componentes cruciales que necesitan cumplir con estrictas especificaciones técnicas y estéticas.
Fabricación de Carcasas
Las carcasas de dispositivos electrónicos, tales como teléfonos móviles, ordenadores y electrodomésticos, son fabricadas a través de este proceso. Gracias a su capacidad para crear formas complejas y detalles precisos, el moldeo por inyección se convierte en la solución ideal para la creación de estuches que protegen los componentes internos y mejoran la apariencia del producto final.
Componentes Internos y Conectores
Además, se producen numerosos componentes internos y conectores para dispositivos electrónicos. La alta precisión necesaria para estos elementos críticos se logra fácilmente con el moldeo por inyección, lo que asegura un montaje eficaz y un funcionamiento fiable de los aparatos electrónicos.
Productos de Consumo y Juguetes
Un ámbito donde el moldeo por inyección ha cobrado especial relevancia es en la fabricación de productos de consumo, incluyendo juguetes, envases y recipientes, lo que permite la producción de objetos atractivos y funcionales en grandes cantidades.
Juguetes
La industria de los juguetes utiliza el moldeo por inyección para producir una amplia gama de productos, desde figuras de acción hasta juegos de construcción. La capacidad de crear formas intrigantes y colores vibrantes atrae a los consumidores y cumple con los estándares de seguridad requeridos para estos productos.
Envases y Recipientes
El moldeo por inyección también se aplica en la creación de envases y recipientes para alimentos y otros consumibles. Este método no solo asegura la producción en masa de envases resistentes y ligeros, sino que también permite la creación de diseños que son funcionales y atractivos para los consumidores.
Industria Médica
En el sector médico, el moldeo por inyección es esencial para la producción de diversos dispositivos y componentes que deben cumplir con los más altos estándares de calidad y precisión.
Dispositivos Médicos
Los dispositivos médicos, incluidos instrumentos quirúrgicos y aparatos diagnosticadores, son fabricados utilizando esta técnica. Los materiales utilizados en estos productos deben ser biocompatibles y cumplir con normativas estrictas, lo que hace del moldeo por inyección el método idóneo por su capacidad de producir componentes exactos y seguros.
Carcasas de Equipos Médicos
La creación de carcasas para equipos médicos, como monitores y máquinas de diagnóstico, también se realiza mediante moldeo por inyección. Estas carcasas no solo protegen los componentes internos, sino que también facilitan la limpieza y el mantenimiento, aspectos cruciales en un entorno médico.
Importancia del Diseño en el Moldeo por Inyección
El diseño juega un papel crucial en el moldeo por inyección, ya que influye directamente en la calidad y funcionalidad de las piezas producidas. Un diseño efectivo no solo optimiza el proceso de fabricación, sino que también permite maximizar el rendimiento del material utilizado.
Consideraciones de Diseño para Moldeo por Inyección
Al desarrollar un diseño para ser moldeado por inyección, es vital tener en cuenta diversos factores que pueden afectar la viabilidad y eficiencia del proceso. Entre ellos se incluyen:
Espesor de Pared: El espesor debe ser uniforme para asegurar un enfriamiento y solidificación adecuados, evitando deformaciones y problemas de calidad.
Radio de Curvatura: Las esquinas y ángulos agudos deben ser redondeados para minimizar tensiones en el material y facilitar la expulsión de la pieza del molde.
Desalineación: El diseño debe permitir un alineamiento perfecto del molde para evitar problemas de cierre que podrían resultar en piezas defectuosas.
Ubicación de Distribución de Material: Se debe prestar atención a los puntos de inyección y a cómo se distribuye el material en la cavidad del molde para asegurar una llenado adecuado y evitar deformaciones.
Características de Diseño: El diseño de características adicionales como inserciones, nervaduras o funciones específicas debe realizarse cuidadosamente, considerando las limitaciones del proceso de inyección.
Herramientas y Software de Diseño
La utilización de tecnologías avanzadas y software específico es fundamental para optimizar el diseño en el moldeo por inyección. Herramientas especializadas permiten a los diseñadores simular cómo se comportará el material, optimizando así cada detalle antes de la producción.
Software CAD: Permiten crear modelos 3D detallados que facilitan el análisis de diseño y la manipulación de geometrías complejas.
Simulación de Flujo: Herramientas que pueden predecir cómo fluirá el material a través del molde, ayudando a identificar y resolver problemas potenciales en la fase de diseño.
Prototipado Rápido: La impresión 3D y otras técnicas de prototipado permiten crear réplicas físicas de diseños para pruebas antes del moldeo definitivo, ahorrando tiempo y recursos.
Optimización del Proceso de Moldeo por Inyección
La optimización del proceso de moldeo por inyección es esencial para mejorar la eficiencia y la calidad de las piezas producidas. A través del análisis de parámetros y el mantenimiento adecuado del equipo, se pueden lograr mejores resultados en la fabricación.
Análisis y Ajuste de Parámetros de Inyección
El análisis y ajuste de los parámetros de inyección son cruciales para asegurar que el proceso se realice de manera eficiente. Los principales parámetros a analizar incluyen:
Presión de inyección: La presión con la que se inyecta la resina influye directamente en la calidad de la pieza. Una presión adecuada evita defectos de llenado y mejora la densidad del material.
Velocidad de inyección: Controlar la velocidad de inyección ayuda a que el material fluya correctamente dentro del molde. Una velocidad incorrecta puede causar problemas de fricción y dañar el molde o afectar la pieza.
Temperatura del material: La temperatura a la que se funde la resina debe ser óptima. Un calentamiento excesivo puede descomponer el material, mientras que uno insuficiente puede dificultar el llenado del molde.
Tiempo de enfriamiento: Determinar un tiempo de enfriamiento adecuado es fundamental para asegurar que la pieza tenga la resistencia necesaria. Un enfriamiento rápido puede causar tensiones internas, mientras que uno excesivamente largo puede aumentar el ciclo de producción.
Tiempo de ciclo: Minimizar el tiempo de ciclo sin comprometer la calidad es crucial para la eficiencia del proceso. Un análisis detallado de cada fase del ciclo permite decisiones informadas sobre ajustes necesarios.
Mantenimiento y Mejora del Equipamiento
El mantenimiento regular del equipamiento es clave para garantizar un funcionamiento fiable y eficiente. Las áreas a considerar incluyen:
Inspección periódica de componentes: Revisar regularmente partes críticas como la unidad de inyección, la unidad de sujeción y los moldes. Esto ayuda a identificar desgaste o daños que podrían afectar la producción.
Limpieza de moldes: Mantener los moldes limpios evita la acumulación de residuos que pueden provocar defectos en las piezas. La limpieza adecuada también prolonga la vida útil de los moldes y mejora la calidad de las piezas moldeadas.
Actualizaciones tecnológicas: La incorporación de tecnología avanzada, como sistemas de control CNC, permite un mayor control sobre el proceso y mejora la precisión de las piezas. Invertir en actualizaciones regulares es beneficioso a largo plazo.
Formación del personal: Capacitar a los operadores sobre el manejo y mantenimiento del equipo es esencial. Un personal bien formado puede identificar problemas de manera temprana y aplicar soluciones eficaces.
Registro de mantenimiento: Llevar un registro detallado de las actividades de mantenimiento permite identificar patrones de fallos y planificar acciones preventivas que aseguran la continuidad del proceso de producción.
Casos de Estudio y Ejemplos de Aplicación
El moldeo por inyección es una técnica versátil que ha encontrado su camino en diversas industrias. A continuación se presentan algunos casos de estudio que destacan su efectividad y aplicaciones en diferentes sectores.
Éxitos en la Automoción
En el sector de la automoción, el moldeo por inyección ha permitido la producción de una variedad de componentes que son esenciales para el funcionamiento de los vehículos. Aspectos destacados incluyen:
Carcasas de Sistemas Electrónicos: Se utilizan en componentes vitales como unidades de control del motor y sistemas de conectividad.
Conectores Eléctricos: Los conectores moldeados ofrecen alta precisión y resistencia, cruciales para asegurar la fiabilidad de las conexiones eléctricas en automóviles.
Componentes Estéticos: Elementos interiores y exteriores como paneles y molduras que se benefician de la flexibilidad de diseño que ofrece este proceso.
Innovaciones en Productos Electrónicos
El uso del moldeo por inyección en la industria electrónica ha permitido no sólo reducir costes, sino también mejorar la funcionalidad y estética de los dispositivos. Algunos ejemplos de innovación incluyen:
Carcasas de Dispositivos: Se producen carcasas delgadas y ligeras que protegen componentes internos mientras se mantienen en diversos colores y acabados.
Componentes Internos: El proceso permite fabricar piezas de precisión que se integran dentro de circuitos y dispositivos electrónicos.
Conectores y Adaptadores: Se crea una amplia gama de conectores que cumplen con las especificaciones técnicas requeridas por los usuarios y fabricantes.
Producción en Masa de Productos de Consumo
La fabricación de productos de consumo mediante moldeo por inyección se ha convertido en un estándar en la industria. Este método permite productos en grandes volúmenes con la siguiente diversidad:
Envases y Recipientes: Se fabrican envases de plástico para alimentos y productos de limpieza que son seguros y funcionales.
Juguetes: La creación de juguetes a través de moldeo por inyección asegura la producción en masa de artículos con formas y colores atractivos.
Útiles de Cocina: Se desarrollan utensilios de cocina duraderos y de fácil limpieza, moldeados para la comodidad del usuario.
Preguntas Frecuentes sobre Moldeo por Inyección
El moldeo por inyección es una técnica ampliamente utilizada en la fabricación de piezas de plástico. A continuación, se presentan algunas de las preguntas más frecuentes sobre este proceso, que abordan aspectos clave y conceptos esenciales relacionados con su uso y aplicación.
¿Qué Plásticos se Pueden Moldear por Inyección?
El moldeo por inyección es compatible con una variedad de plásticos, siendo los termoplásticos los más utilizados. Entre los tipos de plásticos que se pueden moldear por inyección se incluyen:
Polietileno (PE): Conocido por su versatilidad y resistencia química, se utiliza en productos de consumo y en envases.
Polipropileno (PP): Destacado por su flexibilidad y resistencia, ideal para envases alimentarios y componentes industriales.
Acrilonitrilo Butadieno Estireno (ABS): Este material es duradero y ligero, frecuentemente empleado en juguetes y elementos de automoción.
Policarbonato: Con propiedades ópticas y resistencia a impactos, se usa en aplicaciones como lentes y carcasas electrónicas.
Nailon: Apreciado por su resistencia y propiedades eléctricas, es común en maquinaria y artículos deportivos.
¿Cuáles son las Principales Ventajas del Moldeo por Inyección?
Este proceso ofrece varias ventajas que lo convierten en una opción preferida para la producción en masa de piezas de plástico. Entre estas ventajas se encuentran:
Alta Precisión: Permite producir piezas con tolerancias ajustadas y mínimas imperfecciones.
Capacidad de Producción en Masa: Ideal para fabricar grandes volúmenes de productos en tiempos reducidos.
Flexibilidad de Diseño: Posibilita la creación de formas complejas y diseños intrincados.
Diversidad de Materiales: Se pueden utilizar diferentes tipos de plásticos, lo que amplía las posibilidades de aplicación.
Eficiencia Económica: Aunque la inversión inicial en moldes puede ser alta, los costos por pieza disminuyen en producciones masivas.
¿Qué Factores Afectan la Calidad de las Piezas Moldeadas?
La calidad de las piezas obtenidas mediante el moldeo por inyección puede verse influenciada por varios factores. Entre los más significativos se encuentran:
Selección de Material: La elección del tipo de plástico puede impactar las propiedades finales de la pieza.
Temperatura de Fusión: Un control adecuado de esta temperatura es crucial para evitar defectos en el producto.
Parámetros de Inyección: La presión y velocidad de inyección deben ajustarse correctamente para obtener un llenado uniforme del molde.
Tiempo de Enfriamiento: Un enfriamiento inadecuado puede ocasionar deformaciones o tensiones internas en la pieza.
Mantenimiento de Moldes: La precisión en la fabricación y el cuidado de los moldes es esencial para garantizar la calidad constante de las piezas.
¿Cómo se Selecciona el Material Adecuado para una Pieza?
La selección del material adecuado es un aspecto crucial en el moldeo por inyección. Para elegir el plástico ideal para una pieza, se deben considerar varios factores:
Propiedades Mecánicas: Se debe analizar la resistencia, dureza y flexibilidad necesarias para la aplicación final del producto.
Resistencia Química: Es importante considerar la exposición a diferentes sustancias químicas en el entorno donde se utilizará la pieza.
Condiciones de Uso: Las temperaturas y condiciones ambientales a las que estará sometida la pieza influencian la elección del material.
Coste y Disponibilidad: La viabilidad económica del material y su disponibilidad en el mercado deben ser evaluadas.
Procesabilidad: Se deben considerar las características de procesado del material para asegurar una producción eficiente.
Contacto
alcoy@frogplastics.es
Horario de oficina:
Lunes a Jueves: De 8:00h a 18:00h
Viernes: De 8:00h a 15:00h
Oficina: (+34) 631 687 558
FROG PLASTICS S.L
Llámenos ahora y le atenderemos personalmente, o si lo prefiere, envíenos un whatssap o e-mail y le contestaremos a la mayor brevedad posible.
NIF B-56540388
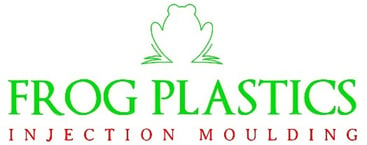
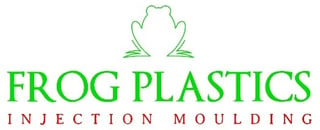
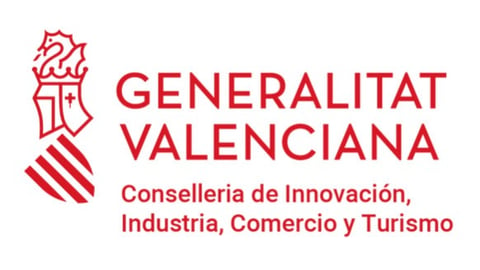
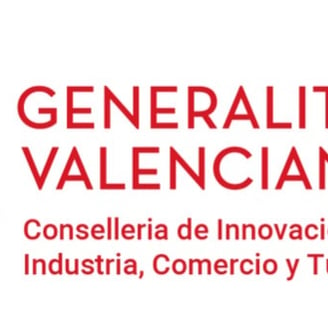
Proyecto subvencionado por la Conselleria de Innovación, Industria, Comercio y Turismo:
“FROG PLASTICS, S.L.” ha participado en el programa de Ayudas para apoyar las inversiones productivas realizadas por las pymes de diversos sectores industriales de la Comunitat Valenciana. RESOLUCIÓN de 15 DE febrero de 2024 (DOGV Num. 9791 / 19.02.2024) a través de la inversión para el proceso de fabricación de piezas por inyección de plástico
Año: 2024 Número de expediente: INPYME/2024/414
Subvención: 34.935,45 €